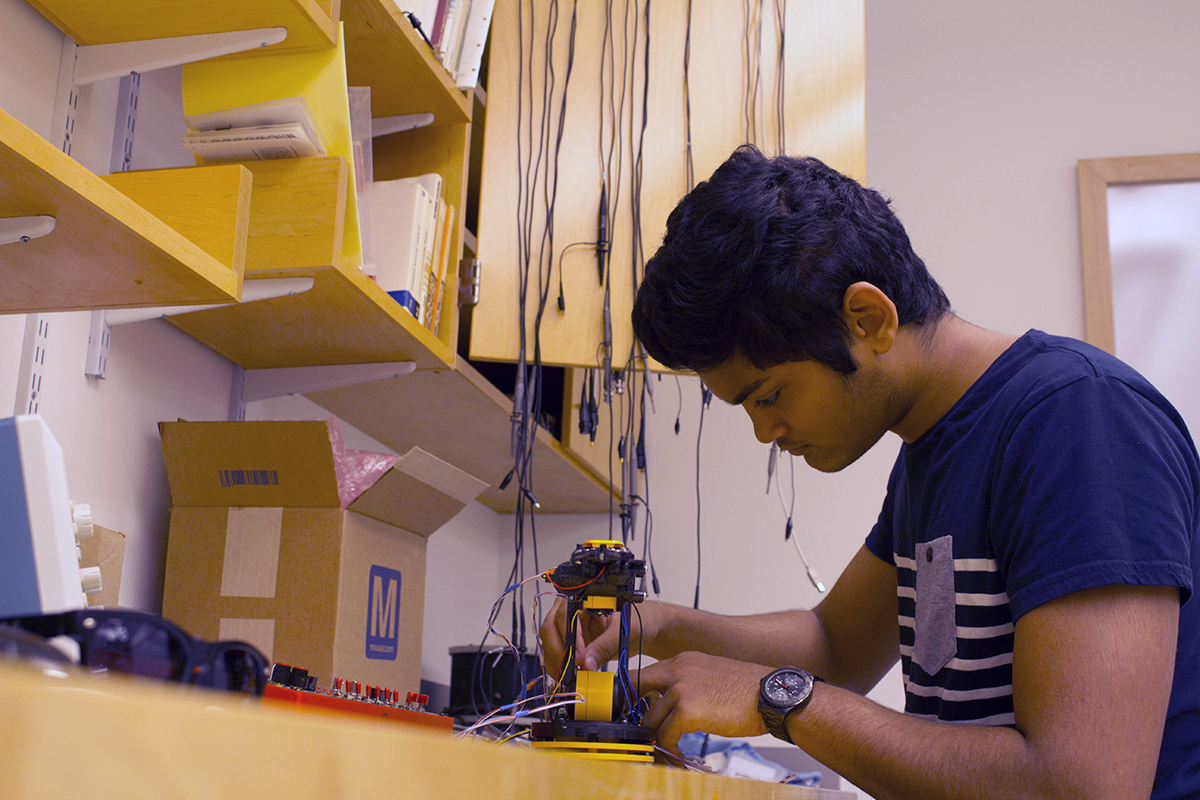
Steven Laurent Cunden ’18 is this summer helping to further develop the robotics technologies used in the Physics 245 course, Electronics and Computers. Cunden is working with the class instructor, Associate Professor of Physics Brian Collett, on enabling the relatively simplistic robotic arms used in the course to receive and react to positional feedback.
“(The robotic arms) are very simple,” explained Cunden, “consisting of five motors simulating a human arm.” Through coding and programming the arms are capable of performing simple tasks, such as picking up and moving objects, but are limited due to their inability to recognize their geographic position relative to a given starting point. Given the lack of positional feedback, the arms cannot be zeroed effectively as they lack an origin, or reference point from which they can measure deviations. In order to record the movement of the arms, said Cunden, “students usually just record the amount of time the arm is in motion, but that leads to problems due to gravitation.”
He explained that very small errors occur when using the timing method, as due to the force of gravity, the arm will not move exactly the same distance up that it will moving down in the same amount of time. These very small errors, while seemingly minute, stack up to create undesirable inaccuracies in large numbers.
Providing the arms with positional feedback, however, can be a complicated affair. “The arm is no more than a foot and a half,” said Cunden, “so you don’t want to keep adding devices, or alter the exterior too much.” To address this, Cunden is working with QR113 optical sensors, sensors usually utilized in larger robotics setups, which are light sensitive and give different feedback, in the form of pulses, based on how light or dark a given input is. These sensors are then paired with a patterned gear, called an encoder shaft or encoder gear - essentially a circle divided into 40 sections that alternate between black and white.
With this setup, when the arm moves, the gear moves accordingly, and a computer records the number of pulses given off by the sensors. The number of pulses in turn indicates the number of black and white sections on the encoder gear that were passed, and therefore the number of degrees that the arm has rotated. One pulse indicates a rotation of 9 degrees, two pulses indicates 18 degrees, and so on. An additional gear is then superimposed upon the encoder gear, divided into only two sections, that in turn provides an anchor point for the arm, and cuts down on small deviations such as missed pulses that could jeopardize the collected data. “We’ve made one simplistic arm and one advanced arm, and we plan to keep advancing the newer arm,” claimed Cunden, “but it was all possible due to the positional feedback, (and) the arm doesn’t really look any different with the addition of the optical sensors.”
Cunden expressed great satisfaction with both his work, as well as his first foray into the field of robotics more broadly. “Before doing this research project, my focus was nuclear physics,” he explained. “But this project has made me start looking into the robotics field. My career prospects have completely changed, and I’m now mostly considering robotics engineering for graduate school.”